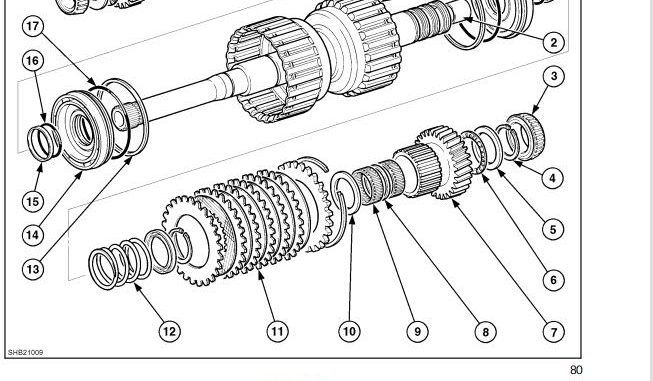
How to remove New Holland b115 gearbox gear
CNH DPA5 Adapter New Holland Heavy Duty mechanical Diagnostic Tool – full chipsINPUT SHAFT DISASSEMBLY (FRONT SUPPORT END)
IMPORTANT: When using a bearing puller be very careful to ensure it does not touch the tip of the gear teeth as they may become chipped or broken.
1. Support the shaft vertically (rear support end) in a soft jawed vice and remove the sealing ring. Attach a 3 legged puller (1), to the underside of the forward primary gear (2) and remove the gear hub, needle bearings and spacer, thrust washer, and bearing from the shaft.
NOTE: Prior to removal of the snap ring the wear factor of the clutch plates should can be checked.
Measure the distance between the face of the top plate to to underside of retainer, approx. dimensions:
When new Approx. 2.22–4.93mm (0.08–0.19in)
When run in Approx. 5.64–8.35mm (0.22–0.32in)
Anything exceeding or close to 8.35mm should be considered as worn and replaced with new.
2. Release the snap ring (1), retaining the clutch pack drive rings and remove from the clutch housing.
The discs must be flat and not discoloured in any way, if in doubt renew the discs.
3. Using a press and tool NH 21 102 (1), compress the clutch piston spring (2) to enable release of the circlip (3). Carefully release the press pressure on the spring. Remove the circlip, washer and spring.
42 SECTION 21 — TRANSMISSIONS — CHAPTER 1
05/2003
4. To remove the piston blank off the oil feed holes that are not required and carefully apply air pressure to the forward clutch oil feed hole (1) in the middle ring sufficiently to push the piston out against seal resistance.
How-to-remove-New-Holland-gearbox-gear-8
5. The piston seals should be removed and discarded prior to re–assembly.
Inspect all parts for scoring wear marks and or discolouration, replace suspect parts as necessary.
2023 CASE New Holland Electronic Service Tools (CNH EST v9.8) Engineering Diagnostic Software
NOTE: The grove depth on the friction disc when new is 0.38mm (0.014in) and is acceptable down to 0.10mm (0.004in). However any depth close to or below 0.10mm (0.004in) when a teardown has taken place should be considered as worn and replaced with new.
INPUT SHAFT RE–ASSEMBLY (FRONT SUPPORT END)
With the shaft supported vertically (in a soft jawed vice), re–assembly is in reverse order of disassembly, ensure all metallic parts are liberally coated in clean transmission oil before fitting.
How-to-remove-New-Holland-gearbox-gear-9
6. The internal and external piston seals require replacing, before assembly, soak seals in luke warm water prior to fitting. Carefully refit the inner ‘O’– ring and then the gland seal. The outer ‘O’– ring can now be fitted along with the outer gland seal.
How-to-remove-New-Holland-gearbox-gear-10
7. Lubricate the piston seal and carefully place the piston back into the clutch housing until fully seated. Re–assemble the piston spring, washer and compress using tool no #380000679 sufficiently to allow refitting of the circlip and place the thrust washer in position.
IMPORTANT: Soak new clutch friction discs in clean new oil for a minimum of 3 hours
How-to-remove-New-Holland-gearbox-gear-11
8. Continue to refit the clutch discs (6 thin steel with 1 thick retaining plate) and (6 friction plates) back into the hub, steel first, followed by friction and then repeat steel, friction. The final steel plate to be fitted is the thicker retaining plate that the snap ring seats onto. Refit the snap ring into the groove of the clutch hub.
9. Once the gear is assembled into the clutch plates the needle bearings and spacer can be assembled into the bore of the gear without removing it from the clutch drum.
10. Place the thrust bearing (1) on the gear face with the thrust washer and refit the bearing using apress and tool #380000712 (2).
SECTION 21 — TRANSMISSIONS — CHAPTER 1
05/2003
11. With the bearing (1) fully seated ensure a freeplay of at least 0.0508–0.40mm (0.002–0.016in) exists between the thrust washer and gear (2).
12. Fit a new sealing ring onto the shaft above the
bearing (1).
INPUT SHAFT DISASSEMBLY
(REAR SUPPORT END)
13. Support the shaft vertically (front support end) in a soft jawed vice and remove the sealing rings (1). Attach puller (2) to the underside of the bearing (3) and remove. Remove the circlip which allows the removal of the thrust washer, thrust bearing, gear/hub, needle bearings with spacer.
New Holland AG & CE Service Manuals PDF 2019 Download (170GB)
14. Release the snap ring (1) retaining the clutch
pack drive discs and remove from the clutch
housing.
SECTION 21 — TRANSMISSIONS — CHAPTER 1
15. Using a press and tool # 380000679 compress the clutch piston spring to enable release of the circlip. Carefully release the press pressure on the spring. Remove the circlip, washer and spring