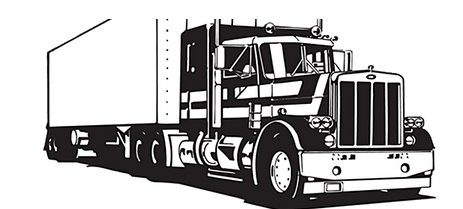
JCB Common Rail Fuel Codes
The electronic engine control unit (ECU) and devices connected to it are distinguished by their robust construction and are basically more reliable than connecting wires and connectors.
BEFORE checking or replacing electrical devices, make sure that the appropriate wires and connectors are installed and that they are functioning properly. In many cases, electrical faults are easily fixed by identifying faulty wires,
connectors or ground points. Before performing work, it is necessary to disconnect the electrical system by disconnecting the battery. Check the relevant machine documentation for the correct procedure.
1 ELECTRICAL WIRING HARNESS – Visually inspect the connecting wires and connectors for signs of damage.
Check out the following aspects:
a Shabby wires – periodic short circuits.
b Cut wires – open circuits. A likely cause is the ingress of wires into the mechanical mechanisms of the machine.
c Broken wires – open circuits. The probable cause is incorrect laying or linking of wires without enough slack for the machine to move.
d Flamed wires – periodic short circuits. A likely cause is contact with the turbocharger or exhaust system.
2 CONNECTORS – Visually inspect the corresponding connectors. Check out the following aspects:
a Connection – Periodic short circuits. Make sure that the connectors are correctly connected and that their locking mechanisms are locked.
b Damage – intermittent open circuit or short circuit. Inspect the connectors for signs of physical damage (such as broken housings or retainer clips). Upon contact with a hot exhaust system or turbocharger, the connectors may also melt. Disconnect the connectors and inspect the pin contacts for damage (e.g., corroded, bent, or broken pin contacts). DO NOT TOUCH the pin contacts of the connector on the electronic engine control unit (ECU). Broken connectors must be replaced.
c Pollution – intermittent open circuit or short circuit. Disconnect the connectors and inspect their interior for contamination (usually water, oil, or hydraulic fluid). If necessary, clean the pin pins of the connector and the socket with a cotton swab or similar object. DO NOT TOUCH the pin contacts of the connector on the electronic engine control unit (ECU). If there are clear signs of water contamination, the connectors must be allowed to dry completely before connecting. Carefully inspect all sealing elements for signs of contamination or damage.
3 Ground Points — Locate the ground points on the engine and machine. Make sure the wire terminals are connected correctly.
Fault Codes – Structure
The structure of the DTCs, also known as Diagnostic Trouble Codes (DTCs), has been standardized and represented by a 7-digit code for all road and off-road vehicles and vehicles. According to the standard (called J2012), all DTCs must follow the structure below.
1st character – defines the vehicle system (e.g. P = power train, C = chassis, U = network)
2nd and 3rd characters – define the subsystem (transmission, CAN network, brakes, etc.)
4th and 5th symbols – identify a specific component, circuit or fault (e.g. starter relay)
6th and 7th characters – are called “fault type bytes” (FTB) and indicate a specific fault (for example, 11 = short circuit to ground). For a complete listing, see FTB Numbers below.
Some special fault codes are defined by an international standard, while others can be determined by individual vehicle manufacturers.
Depending on the specification of the machine, there are several ways to access and display fault codes that are recorded by the engine ECU:
CAN Bus Display
The machine can be equipped with a CAN-bus based display. Such a display may show all registered codes, for example, P0047. All registered codes will be displayed. The operator may be able to erase the fault code log. For more information, see the relevant machine documentation.
Computer connected to CAN bus
Access to the registered error codes can be provided using a suitable laptop on which the appropriate diagnostic software is installed, for example, the engine diagnostic tool JCB 444 Engine Diagnostics. The computer must be connected to the machine’s CAN bus socket using a data transfer adapter (DLA).
After connecting, all registered codes can be displayed. The engineer also has the opportunity to erase the fault code log.
Fault Byte Number (FTB) Numbers
00 No subtype information
02 General fault with signal
04 Internal system fault (ECU)
07 Mechanical failure
05 System programming failure
09 Component malfunction
11 Short to ground (SC2G)
12 Battery short circuit (SC2VBAT)
13 Open circuit (OS)
16 Circuit voltage below acceptable threshold
17 Circuit voltage above acceptable threshold
18 Circuit current below acceptable threshold
19 Circuit current above acceptable threshold
1A Circuit Resistance Above Threshold
1B Circuit resistance below acceptable threshold
1C Circuit voltage out of range
1F Intermittent circuit
23 Constantly low signal
24 Constantly high signal
26 Rate of change of signal below acceptable threshold value
27 The rate of change of the signal is above an acceptable threshold value
29 Invalid signal
2F Volatile Signal
31 No signal (skipped / missing)
36 Signal frequency too low
37 Signal frequency too high
38 Wrong signal frequency
45 Program memory failure
46 Calibration / parameter memory failure
47 Malfunction of self-monitoring system / microcontroller / microprocessor
4B temperature rise
54 No calibration
64 Malfunction of signal acceptability
62 Signal comparison failure
72 Actuator stuck open
73 Actuator stuck closed
71 Actuator stuck
81 Received network data contains error
85 Signal out of range
86 Invalid CAN signal
88 BUS OFF
9A Operating conditions for a component or system
92 Performance or malfunction
96 Component malfunction or internal malfunction
97 Component or system is obstructed or blocked
98 Temperature rise of a component or system
If a malfunction is detected, the computer determines the severity of the malfunction and can take measures to protect the engine or machine from potential damage.
An ECU can take one of four of the following actions:
Inaction
The computer has decided that there is no direct risk to the engine or machine and that the engine is operating normally. Nevertheless, measures should be taken to rectify the malfunction as soon as possible.
Low Torque Mode:
The engine output is reduced in order to reduce the voltage and temperature of the engine, and to minimize its damage. Machines should be stopped at the earliest opportunity to prevent further damage.
Emergency mode of movement to the place of repair work:
Engine output is limited and engine speed is reduced to reduce engine voltage and temperature, and to minimize damage to the engine. Stop the machine as soon as possible to prevent further damage.
Engine muffling / delayed engine muffling
The engine control unit automatically shuts off the engine to prevent an impending failure.
Fault Codes – Numeric List
• Click on the DTC to go to the specific device information and troubleshooting procedure.
P0001 The control circuit of the fuel volume regulator is open
P0002 Range / Performance of the fuel volume regulator control circuit
P0003 Low signal of the control circuit of the fuel volume regulator
P0004 High signal volume control circuit of the fuel volume regulator
P0016 Relationship between the position of the crankshaft and the position of the camshaft
P0087 Too low pressure in the fuel line / system
P0088 Too high pressure in the fuel line / system
P0089 Fuel Pressure Regulator 1 Performance
P0090 The control circuit of the fuel pressure regulator 1 is open
P0091 Low signal control circuit of the fuel pressure regulator 1
P0092 High signal of the control circuit of the fuel pressure regulator 1
P0095 Intake Air Temperature Sensor 2 Circuit
P0096 Intake Air Temperature Sensor 2 Range / Performance
P0097 Low signal circuit intake air temperature sensor 2
P0098 High Intake Air Temperature Sensor 2 Circuit
P0099 Intermittent / erratic intake air temperature sensor 2 circuit
P0105 Manifold Absolute Pressure / Barometric Pressure Circuit
P0106 Range / Performance of the manifold absolute pressure / barometric pressure circuit
P0110 Intake Air Temperature Sensor 1 Circuit
P0111 Low signal circuit intake air temperature sensor 1
P0124 High signal circuit intake air temperature sensor 1
P0113 High signal circuit intake air temperature sensor 1
P0115 Circuit 1, engine coolant temperature sensor
P0116 Range / Performance of circuit 1 of the coolant temperature sensor
P0117 Low signal circuit 1 of the engine coolant temperature sensor
P0118 High signal circuit 1 temperature sensor engine coolant
P0120 Throttle / Pedal Position Sensor / Switch A Circuit
P0121 Range / Performance of “A” Sensor / Throttle / Pedal Position Switch
P0180 Circuit “A” fuel temperature sensor
P0181 Range / Performance of the fuel temperature sensor circuit “A”
P0182 Low signal circuit A “fuel temperature sensor
P0183 High signal circuit “A” fuel temperature sensor
P0190 Circuit “A” of the fuel pressure sensor in the highway
P0191 Range / Performance of circuit “A” of the fuel pressure sensor in the line
P0192 Low signal circuit “A” of the fuel pressure sensor in the highway
P0193 High signal circuit “A” of the fuel pressure sensor in the highway
P0194 Intermittent / unstable signal of the circuit “A” of the fuel pressure sensor in the highway
P0200 Injector circuit open
P0201 Injector circuit open – 1st cylinder
P0202 Injector circuit open – 2nd cylinder
P0203 Injector circuit open – 3rd cylinder
P0204 Injector circuit open – 4th cylinder
P0205 Injector circuit open – 5th cylinder
P0206 Injector circuit open – 6th cylinder
P0218 Transmission Fluid Over Temperature
P0220 Circuit “B” of the sensor / switch throttle / pedal position
P0236 Range / Performance of circuit “A” of turbocharger / supercharger boost sensor
P0252 Range / Performance “A” of the fuel pump fuel meter (cam / rotor / injector)
P0253 Low signal “A” of the fuel metering device of the high pressure fuel pump
(camshaft / rotor / injector)
P0254 High signal “A” fuel metering pump fuel (cam / rotor / injector)
P0261 Low signal of the injector circuit of the 1st cylinder
P0262 High signal injector circuit 1 cylinder
P0263 Deposit / balancing of the 1st cylinder
P0264 Low signal of the injector circuit of the 2nd cylinder
P0265 High signal circuit injector 2nd cylinder
P0266 contribution / balancing of the 2nd cylinder
P0267 Low signal of the injector circuit of the 3rd cylinder
P0268 High signal circuit injector 3rd cylinder
P0269 Contribution / balancing of the 3rd cylinder
P0270 Injector 4 Low Signal
P0271 High signal injector circuit 4th cylinder
P0272 Deposit / balancing of the 4th cylinder
P0273 Low signal of the injector circuit of the 5th cylinder
P0274 High signal injector circuit 5th cylinder
P0275 Contribution / balancing of the 6th cylinder
P0276 Low signal of the injector circuit of the 6th cylinder
P0277 High signal circuit injector 6th cylinder
P0278 Contribution / balancing of the 6th cylinder
P029A The balancing of the 1st cylinder by fuel production is at the maximum limit
P029B The balancing of the 1st cylinder by fuel production is at the minimum limit
P029E The balancing of the 2nd cylinder by fuel production is at the maximum limit
P029F The balancing of the 2nd cylinder by fuel production is at the minimum limit
P02A2 The balancing of the 3rd cylinder by fuel production is at the maximum limit
P02A3 The balancing of the 3rd cylinder by fuel production is at the minimum limit
P02A6 Balancing of the 4th cylinder by fuel production is at the maximum limit
P02A7 Balancing of the 4th cylinder with fuel production is at the minimum limit
P02A8 Balancing of the 5th cylinder by fuel production is at the maximum limit
P02A9 Balancing of the 5th cylinder by fuel production is at the minimum limit
P02A10 The balancing of the 6th cylinder by fuel production is at the maximum limit
P02A11 The balancing of the 6th cylinder by fuel production is at the minimum limit
P02EE Range 1 / Injector Circuit Performance
P02EF Range / Performance of the Injector Chain of the 2nd Cylinder
P02F0 Range / Performance of the injector circuit of the 3rd cylinder
P02F1 Range / Performance 4 Injector Circuit
P02F2 Range / Performance 5th Injector Circuit
P02F3 Range / Performance 6th Injector Circuit
P0335 Circuit “A” crankshaft position sensor
P0340 Circuit “A” camshaft position sensor
P0341 Range / Performance of the camshaft position sensor circuit “A”
P0371 Excessive number of pulses “A” signal high-resolution time stamps
P0372 Too low number of pulses “A” signal high-resolution time stamps
P0374 No pulse “A” signal high-resolution time stamps
P0500 “A” vehicle speed sensor
P0501 Range / Performance “A” of the vehicle speed sensor
P0503 Intermittent / unstable / high signal “A” of the vehicle speed sensor
P0520 Low oil pressure warning light control circuit
P0521 Range / Performance of the engine oil pressure sensor / switch
P0522 High oil pressure
P0523 Low oil pressure
P0560 System Voltage
P0562 System Low Voltage
P0563 System High Voltage
P0566 Signal “off” (“Off”) cruise control
P0567 Cruise Control Resume Signal
P0569 Cruise control “Coast” signal
P0570 Cruise Control Accelerate Signal
P0575 Cruise Control Input Circuit
P0602 Control Module Programming Error
P0603 Standby memory error (CAM) of the internal control module
P0604 RAM error (RAM) of the internal control module
P0605 Read-only memory error (ROM) of the internal control module
P0606 Functional malfunction of the security system
P0607 Functional malfunction of the security system
P060A Functional Security Malfunction
P060B Functional malfunction of the security system
P0612 Control circuit of the engine speed relay
P0615 Starter Relay Circuit
P0616 Starter Relay Circuit Low
P0617 Starter Relay Circuit High
P061B Functional malfunction of the security system
P061C Functional malfunction of the security system
P061E Functional malfunction of the security system
P0627 Global Fuel Pump Malfunction – Open Circuit
P0628 Global fuel pump malfunction – short to ground
P0629 Global fuel pump malfunction – short to battery
P062B Functional malfunction of the security system
P062D Fuel Injector Control Circuit Performance
P062E Fuel Injector Control Performance
P062F EEPROM error of the internal control module
P0630 VIN code not programmed or incompatible – ECM / PCM
P0641 Circuit “A” of the reference voltage of the sensor is open
P0650 Malfunction Indicator Light (MIL) Control Circuit
P0651 Circuit “B” of the reference voltage of the sensor is open
P0655 Malfunction of the engine test indicator light (CEL)
P0656 output circuit of the fuel level sensor
P0668 PCM / ECM / TCM Internal Temperature Sensor Circuit A Low
P0669 High signal circuit “A” internal temperature sensor PCM / ECM / TCM
P0685 ECM / PCM power relay control circuit open
P0697 Circuit “C” of the reference voltage of the sensor is open
P1101 Positive malfunction of a pressure control error in the line
P1102 Negative malfunction of a pressure control error in the line
P1103 Malfunction of pressure in the line
P1104 Injector Update Failure
P1105 Injector Update Failure
P1106 Injector Update Failure
P1107 Injector Update Failure
P1108 Injector Update Failure
P1109 Injector Update Failure
P110A Injector Update Failure
P110B Injector Update Failure
P1500 Faulty foot choke / pedal – emergency mode of movement to the place of repair work
P1501 Foot Choke / Pedal Failure – Low Torque
P1503 Faulty hand throttle – emergency mode of movement to the venue
repair work
P1504 Manual Throttle Malfunction – Low Torque
P1506 Global Throttle / Pedal Failure – Emergency Travel Mode
repair work
P1509 CAN bus communication error with TSC
P1602 Global Starter Relay Control Circuit
P1603 Functional malfunction of the security system
P1604 Functional malfunction of the security system
P1605 Functional malfunction of the security system
P1606 Functional malfunction of the security system
P2120 Fault channel 1 signal hand pedal
P2125 Malfunction of channel 2 of a signal of a manual pedal
P2135 “A” / “B” Voltage Matching of Throttle / Pedal Position Sensor / Switch
P2138 Hand pedal signal mapping failure
P2147 Malfunction (cutoff) of the injector voltage source
P2148 Malfunction (cutoff) of the injector voltage source
P2226 Chain “A” of the barometric pressure sensor
P2228 Low signal circuit “A” barometric pressure sensor
P2229 High signal circuit “A” barometric pressure sensor
P2264 Sensor circuit for water in the fuel
P2265 Range / Performance of the fuel water sensor circuit
P2266 Low fuel water sensor circuit signal
P2267 High fuel water sensor circuit signal
P2269 State of water in the fuel
P250B Range / Performance Engine Oil Level Sensor Circuit
P256A Idling Sensor / Switch Circuit
open
P256B Range / Performance Sensor / Switch Selector Speed
engine idling
P256C Engine Idle Selector Sensor / Switch Low
P256D High Idle Sensor / Selector Speed Sensor Signal
U0001 High speed CAN data bus
U0073 Bus A of the control module data transmission is off
U0100 Communication failure with ECM / PCM “A”
U0121 Lost Communication With Anti-Lock Brake System (ABS) Control Module
U0401 Invalid data received from ECM / PCM “A”
U3FFF DTC SAE does not exist – specific manufacturer data required
If you need JCB Electronic Service tool, please vist our website https://www.autonumen.com